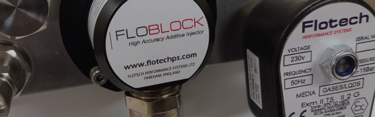
FLOBLOCK injector and FLOBLOCK sensor
As the most advanced additive injection manifold to date, FLOBLOCK combines check valve, needle valve, flowmeter, solenoid valve and filter in a single manifold and integrates with all mainstream load computers, additive controllers, PLC’s and Terminal Automation Systems.
The FLOBLOCK sensor is designed to detect movement of the gears inside the flowmeter section of our FLOBLOCK injectors, for use in hazardous locations.
FLOBLOCK products have been developed in-house by our experts who have more than three decades of experience in additive injection systems.
The FLOBLOCK injector has a unique design and incorporates a number of features:
- Integrated flow control valve allows fine tuning of additive flow and facilitates calibration under true process conditions for more accurate injection rates and reduced additive wastage.
- Integral filter prevents contamination entering the meter or the solenoid.
- Inbuilt non-return valve prevents additive contamination caused by reverse flow.
- One-piece stainless construction & static seals ensures robust, leak-free performance.
- Common bolting pattern and inlet / outlet positions allow direct replacement of most common injectors (adaptors are available where bolting patterns differ).
- Optional dual pulse flow meter provides pulse redundancy to prevent unwanted shutdowns.
- Optional stainless-steel gears and PTFE seals ensure performance across a diverse range of chemicals and additives.
Our FLOBLOCK injector is the most efficient and reliable injector on the market, providing high accuracy and repeatability when injecting additives into fuels and other industrial liquids and gases. We ensure that the FLOBLOCK Sensor is pre-calibrated prior to despatch.
FLOBLOCK injector is held in stock in all derivatives and supported by an extensive spares inventory and expert technical support by our UK facility.
Using the FLOCAL calibration kit (available separately), the FLOBLOCK injector can be quickly, safely and accurately calibrated.
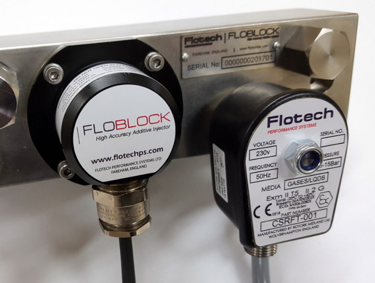
Based upon a product flow rate of 2400 LPM, the Standard Flow Injector is suitable for 100-3000 ppm (typical shot size of 20-200cc). The Low Flow Injector is suitable for 20-600 ppm (typical shot size of 10-40cc).
Applications for the FLOBLOCK injector include:
- Marker Dyes
- DNA Markers
- Performance Additives
- Stenching & Denaturing Agents
FLOBLOCK sensor
The FLOBLOCK Sensor uses hall-effect meter sensors and is pre-calibrated prior to despatch, at this point the K-Factor is determined and tested. This calibration factor (K-Factor) is used by customers equipment for conversion of pulses received to volume dispensed.
When sufficient volume of additive has moved through the FLOBLOCK, the controlling device then turns off the solenoid valve in order to stop flow.
(Note. It is the responsibility of the controlling device, Terminal Automation System (TAS), Preset, or PLC System to perform the algorithms that ratio the additive into the fuel stream properly. If the controlling system is not capable of this level of function, we can also supply complete injection panels that include micro-controllers giving complete injection control.
Explore all our FLOBLOCK datasheets below:
Added value
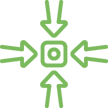
Compact
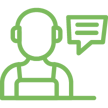
Support
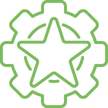
Services
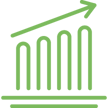
Proven results
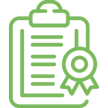
Industry-leading
You might also be interested in...
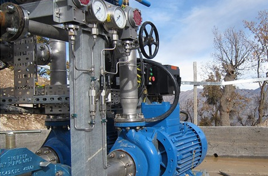
Additive solutions
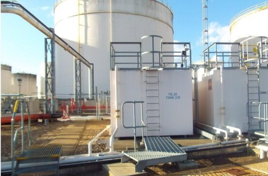
Containerised systems
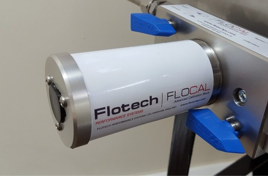
FLOCAL calibration device
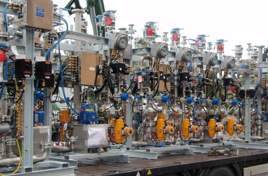
Blending solutions
Here to help with seamless delivery and management of your next process industry project.
Our experts are available to advise, support, and assist with any issues relating to your storage tanks and liquid process infrastructure ensuring you have a safe site, prevent any pollution, and remain operational.
Speak to our experts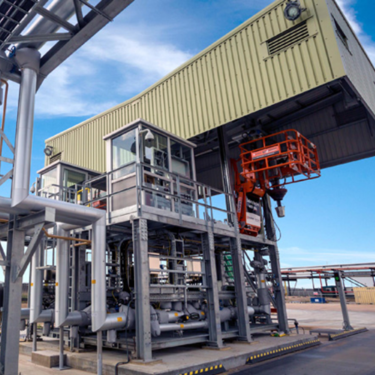