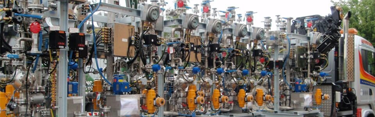
Blending solutions
We help organisations processing industrial liquids and gas to manage blending and pressurisation with custom-engineered fuel blending systems and pump skids.
Our pressurising pump skids ensure a sustained blend pressure to maximise the functions of the blending system and prevent fluctuating blend ratios and off-spec products.
Our fuel blending systems are built to suit the users’ current and future blending requirements, from design to selection of flow meter, control valve and controller.
We have been involved in blending since the introduction of biofuel and ethanol to UK fuel over ten years ago and have a track record in delivering reliable, robust systems for a range of blend constituents.
- Blender pressurising systems are tailored to suit the specific application.
- Our blending skids provide a prefabricated, skid-based solution.
- Dual-pumping technology operates the pumps alternately to extend their life and build in pump failure.
Our solutions include systems for accurately blending or pressurising the following:
- Ethanol Blending
- Biodiesel Blending
- FAME Blending
- Denaturing of Ethanol (Bitrex)
- Butane Blending
- Mid-grade Fuel Blending
- Chemical Blending
- Fertilizer Blending
- HFO bunkering
- High dose additives
Added value
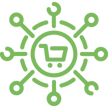
Product selection
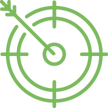
Accurate

Design
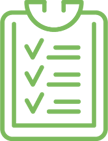
Testing
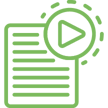
Plug and play
Most of our systems are built off-site in skid form. The advantages of this approach include;
- The system can be piped, cabled and flow tested in advance of delivery.
- Snagging is done off-site which minimises site assembly and start-up time.
- Large skids can be built in modular form to allow road transportation.
- Reduced time on site makes the project cheaper, safer and more convenient.
- All welding, assembly and testing is performed at our fully fitted facility in Hampshire.
- Quality is assured since all welding, pipework and assembly is performed by qualified and experienced personnel.
Blender pressurising systems
These are tailored to suit the specific application, from delivering product to a single blend stream to a fully integrated system to offload, store and pressurise any blend constituent.
Blend pressurising skids are typically fabricated from stainless steel pipework on a galvanized steel frame. Pump and motor selection can accommodate a wide range of applications and blend ratios and a standard configuration includes inlet ball valve, strainer, back pressure control valve, pressure relief valve, pressure gauge, outlet isolation ball valve, motor control centre with heaters and on/off/auto switches.
Our skids can be engineered to incorporate a host of options including:
- Single or dual/redundant pumps
- Motor control and heating
- Temperature monitoring
- Flow monitoring
- Pressure monitoring
- Built in filtration/strainers
- Integrated offloading or loading
- Integrated bunded storage with level monitoring
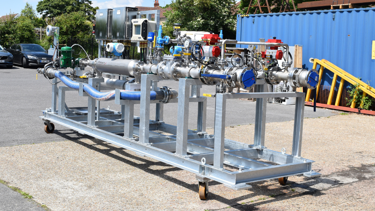
Blending systems
Our blending skids provide a prefabricated, skid-based solution which can accommodate 1-6 blend streams orientated in the vertical or horizontal plane.
Depending up on the application we can offer a host of options including:
- Rack blending or side-stream.
- Single, dual, triple or quad stream options.
- Option integrated pressuring system.
- Integrated or off-skid control system.
- Optional meter proving.
- Integral filtration.
- Temperature and pressure monitoring.
- Customisable for heavy fuel oil or bunkering.
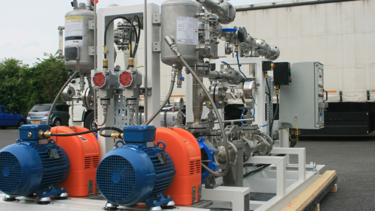
Our status as an independent systems integrator means we can work with specific customer specification, budget and lead time requirements where required. In parallel, we hold strategic distribution partnerships with some of the best equipment manufacturers in the industry so where the specification allows we can gain access to industry leading products at competitive rates.
You might also be interested in...
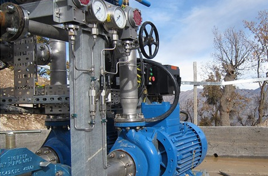
Additive solutions
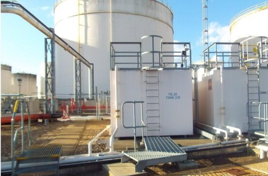
Containerised systems
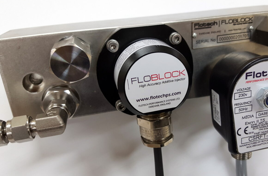
FLOBLOCK injector and sensor
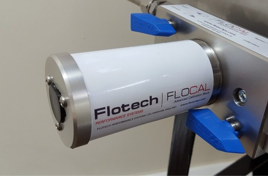
FLOCAL calibration device
Here to help with seamless delivery and management of your next process industry project.
Our experts are available to advise, support, and assist with any issues relating to your storage tanks and liquid process infrastructure ensuring you have a safe site, prevent any pollution, and remain operational.
Speak to our experts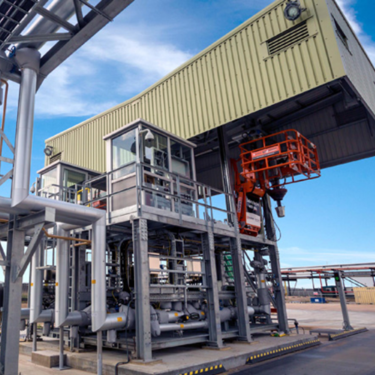